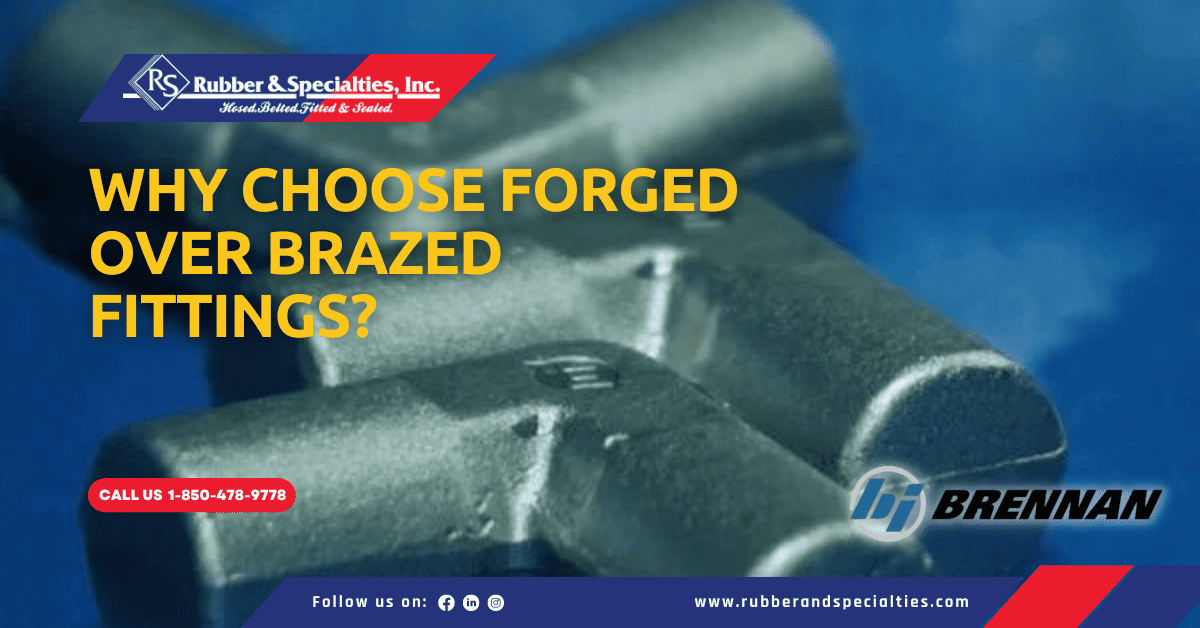
Why Choose Forged Over Brazed Fittings?
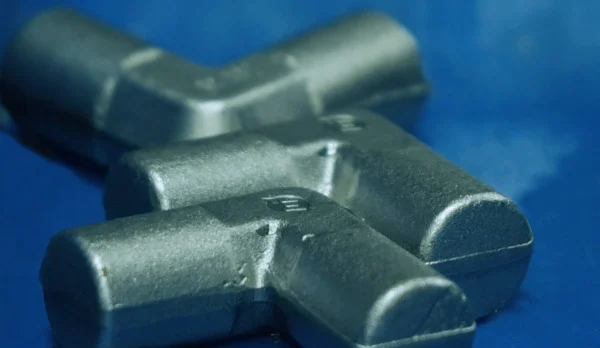
Producing forged steel fittings includes cutting and heating billets, then using a pre-formed die that creates the desired shape under high pressure on the heated billet. The part is then trimmed and shot blasted to remove any flashing. This process produces a machined forged blank fitting to exact net shapes and dimensions.
Forged steel fittings are primarily threaded or socket weld end connections. Forged threaded fittings conform to ASME B1.20.1 and socket weld fittings conform to ASME B16.11.
Common Materials for Creating Forged Fittings:
- Carbon Steel: for forged carbon steel piping components
- Stainless Steel: 304 or 316 stainless steel for corrosive environments and high-pressure applications
Fittings are categorized into two basic geometric categories: straights and shapes:
- Straights are normally machined from cold-drawn hexagonal or round bar stock.
- Shapes are typically forged as described above into one solid piece. Because forged fittings are a single piece, they are no potential leak paths. On the other hand, a brazed fitting made of two or more pieces “brazed together” allows for cracks or other potential leak paths. In addition, due to the brazed fitting’s single-body construction, a forged fitting is much stronger because it does not have a secondary brazed joint. The advantage of a forged piece clearly allows for higher-pressure ratings and longer service life than a brazed fitting.
In the secondary operation, whether straight or shaped (i.e. elbows, tees, etc.) the orifice of the forged piece is then drilled out to the exact ID specification. If it is a threaded fitting the threads are cut to specification. If a socket weld fitting, the forged part serves as the outer body and the ID is drilled to specification.